The Tesla Semi, an all-electric, battery-powered Class 8 semi-truck from Tesla, has been criticized since its unveiling in 2017. Much of the attention has centered on Tesla's claims regarding their Semi's impressive range, thought to be unbelievable with the current state of Li-ion battery technology. Bill Gates famously claimed in his blog post, that all-electric semi-trucks like the Tesla Semi would “probably never” work. Tesla’s recent successful 500-mile demonstration drive showed that critics might have missed something. So, how did Tesla make this work and proved critics to be wrong (once again)?
Below we delve deeper and offer our perspective on that. In the main part, we will give a summary of our analysis, and supplementary is for those willing to nerd it out.
TLDR: it all boils down to (1) increased battery specific energy (35% up from 2017 levels), (2) a higher cruise motor efficiency (90% electric vs 48% diesel, but this one is obvious though), (3) extremely lightweight electric motors, that enabled 3-motor powertrain which led to better energy efficiency at both acceleration and cruise (additional ~2% distance gain for the same pack), (4) efficient aerodynamics (reduction in drag that translates to 25% reduction in energy required for the same distance) and (5) regenerative braking (up to 14% distance gain).
Batteries
While we did not find Tesla’s official comment about the type of batteries that powers the Semi, it's reasonable to assume they are some variant of 2170 nickel-based lithium-ion batteries. They have specific energy near 260 Wh/kg at the cell level. This translates into ~185 Wh/kg at pack level (exact estimates are tricky until Sandy Munro tears down Semi’s battery pack, which we hope happens. Now we can only guess the weight of structure & wiring & cooling). As the total energy capacity of the battery pack is known relatively well (>850 kWh), this results in a total pack weight of more than 4.6 t, more than 20 times the diesel fuel weight needed for a regular truck for the same 500-mile ride. With the technologies available at scale by the time Tesla Semi was unveiled (2017, see, for example, fig. 1 in this reference), the pack weight would be at least 6.2 t.
Powertrain
To convert electric energy to motion, Tesla uses three independent motors, each having approximately 250 kW of power. This is possible thanks to the extremely low weight of each motor (45 kg) and the rest of the drive unit (325 kg), so the total mass of all three motors is still much less than the weight of an average semi truck diesel engine. This design enables having separate engines that are most optimized for different power levels: for acceleration at maximal mechanical power near 750 kW and cruise that requires about 100 kW. We estimate this to have at least a 2% energy efficiency gain, for a detailed breakdown see Supplementary materials.
Weight
The combined weight of the battery and powertrain is dominated by the battery and still exceeds the weight of the diesel engine plus fuel by ~2.5 tons. Considering that electric semis have an extra 2,000 lb (close to 907 kg) of allowed weight and that Tesla Semis’s frame is lighter, freight weight is about the same as that of a regular semi (45,000 lb or 20.4 t).
Aerodynamics
The most important factor here is the optimized aerodynamic shape of the cabin, which reduces the drag force (down to 0.36 compared to typical 0.65) and hence the overall fuel/energy loss by 25% (see supplementary for details). Reduced energy demand leads to lighter battery packs, leaving more space for the freight. But it’s worth mentioning that the same improvement can be applied to regular trucks as well. In this sense, theoretically, the improvement in aerodynamics in itself should not lead to a competitive advantage of electric trucks over their diesel counterparts - we noted this earlier in the context of aviation.
Regenerative braking
Usually, the regeneration factor attracts less attention when comparing internal combustion engines and electric motors, and this could be justified for driving in model conditions at a constant speed. However, in real life, vehicles experience periods of high energy consumption (uphill or acceleration) and periods of low energy consumption when braking (downhill or stopping). During braking, kinetic energy is transformed into heat in brakes/brake pads, while in EV it is partially returned to the battery through recuperation process.
The battery discharge curve in the Tesla Semi test drive (blue curve in the chart below) implies that without regenerative braking (which we can see as blue line going up) the batteries would discharge 70 miles earlier (red curve, which eliminates upward sections). That’s 14% of the distance. Keep in mind that these percentages can be higher/lower, depending on the terrain and traffic.
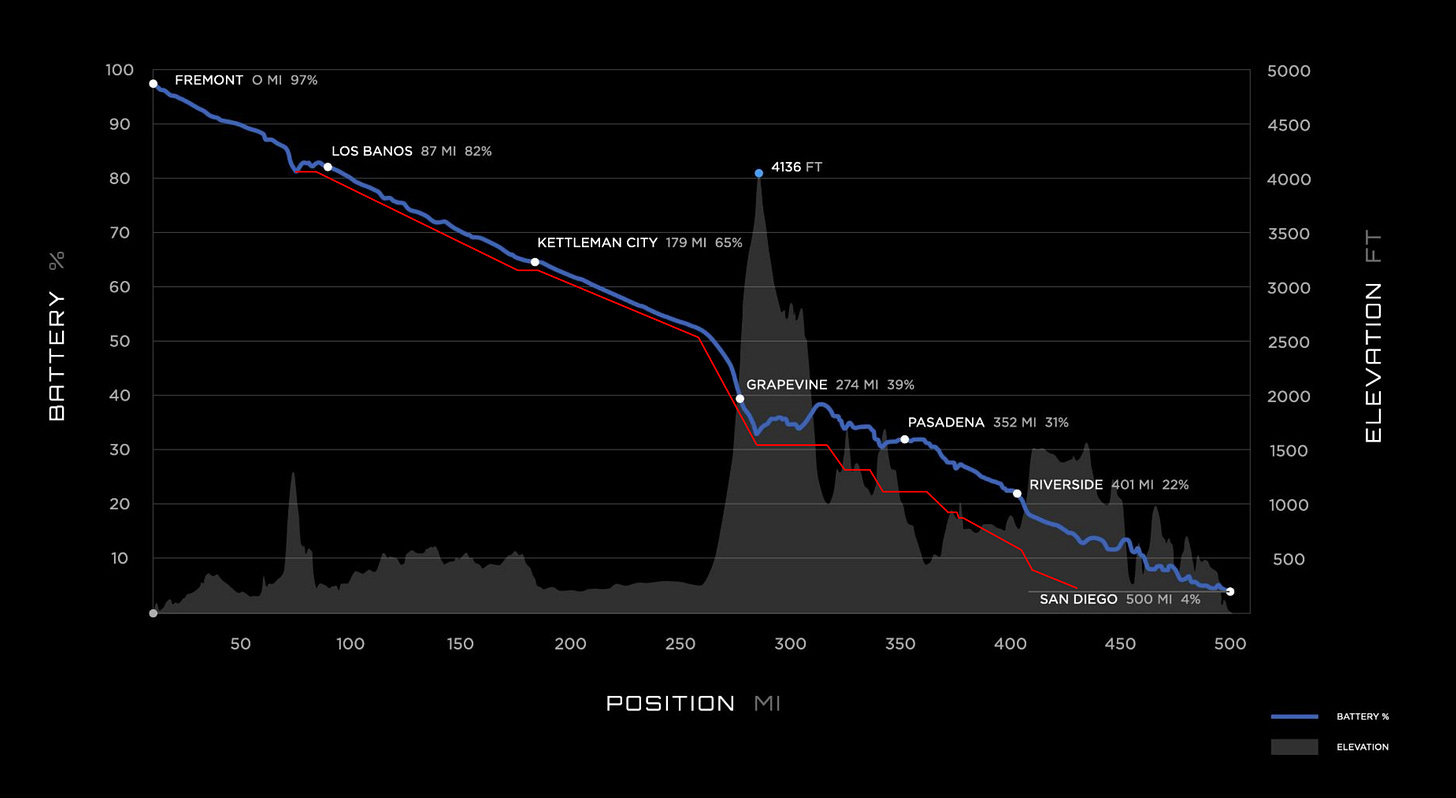
Synergistic effect
To visualize the effect of all of these improvements, let’s compare energy requirements as if we had different combinations of these improvements (graph below).
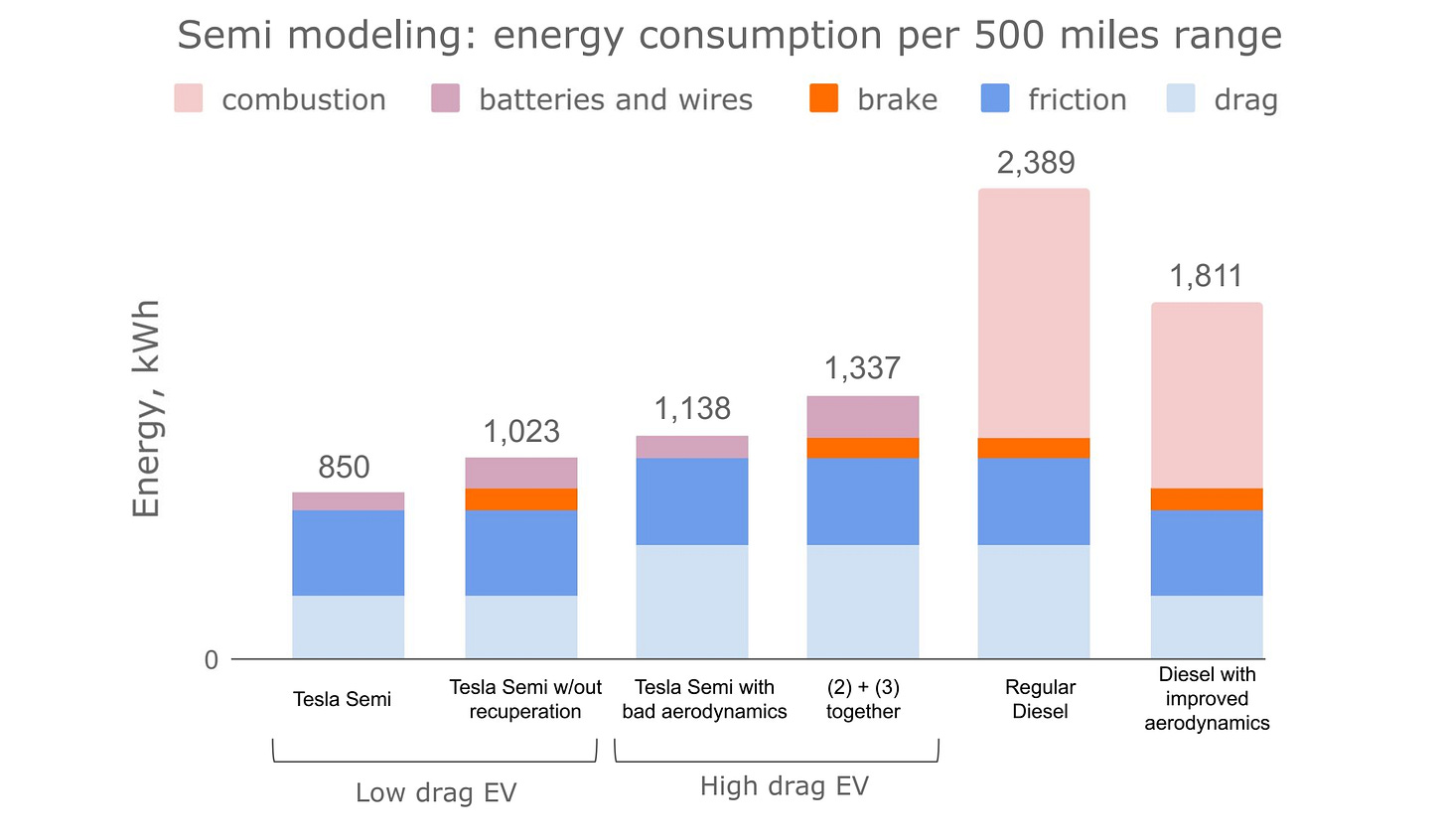
Bonus: any takeaways relevant to electric aviation?
Firstly, Tesla Semi’s power output is comparable to the DHC-6 Series 300 Twin Otter 20-seater utility aircraft (1,014 kW total power from both propellers). Therefore, it can be cautiously assumed that the expected problem with heat removal from the battery assembly at high power during takeoff can be solved at least for a utility aircraft in a way similar to the Tesla Semi’s solution. Of course, that is just an assumption, without a firm conviction, since aircraft batteries for such an aircraft must withstand high power much longer: while the truck's cruising power drops 7.5x down to 100 kW after a short period of acceleration, the utility aircraft's power drops only 2x down to about 500 kW. But Tesla’s success with Semi’s battery pack cooling shall definitely give us some comfort that cooling is solvable (especially if we consider the potential use of outside airflow for cooling).
Secondly, critics of all-electric aviation (EA) often overlook the synergistic effects of small improvements (same as Semi’s critics did). It's about optimizing the entire vehicle system to maximize efficiency. The Tesla Semi's impressive range and efficiency aren't the product of one breakthrough technology but rather the result of multiple interlinked technologies and design strategies. Of course, we can’t compare EAs and EVs directly (for one, drag does not depend on mass for EVs but does for an aircraft), but we still can learn some lessons:
battery technologies will make further progress: what is impossible now can become a reality in 5 years (our consultations with experts show that we can expect as high as 500-550 Wh/kg for Li-ion);
lightweight electric engines could enable what was impractical with internal combustion (distributed propulsion or separate engines for take-off and cruise);
improved aerodynamics (Lift-to-drag optimization through aircraft geometry, laminar flow, etc) is a key enabler;
the battery weight could be partly offset by the optimized airframe;
high power at take-off is a solved problem at least for 1 MW;
there are feedback loops that allow these factors to reinforce one another.
These lessons tell us again, that retrofit is not the way to adapt electric propulsion. In our future posts on the topic, we will explore what the aircraft of the future may look like. So, subscribe and stay tuned!
P.S.: And of course if you want to dive even deeper into this topic, feel free to check out the details of our calculations/sources below.
Supplementary
Batteries
In the main text, we assumed that Tesla uses 2170 nickel-based lithium-ion cells for their Semi. Tesla has been developing more advanced battery technologies, notably the new 4680 cells announced at their Battery Day event in 2020, but those cells are not currently used in Semi. These cells promise 54% improvements in energy density, which could add as much as 54% to the Semi's impressive range in the future.
Nickel-based Li-ion cells that are currently used in Model S have a specific energy of 260 Wh/kg at the battery level and more than 185 Wh/kg at the pack level. We take this as an approximation, but we shall expect the real number to be different as its wiring, cooling, and structure will be different. For a rough estimate of the battery pack weight, we use the total usable energy stored in the battery back, which is more than 850 kWh (provided the range (500 mi) and energy consumption (1.7 kWh/mi) claimed by Musk). This corresponds to a total weight estimate for the battery of 4.6 metric tons (more than 20 times the diesel fuel weight of a regular Semi truck). A 300-mile version of the Tesla Semi is also to be produced, but we focus on the more powerful option, to see where the technology is practically limited today.
Powertrain
At the Tesla Semi Delivery event in December 2022, Musk presented the details of the truck’s powertrain, which resembles the Model S tri-motor, each unit having approximately the power of 250 kW. This design allows having separate engines that are optimized for their tasks: 2 units for acceleration from 0 to 60 mph in 20 seconds at full weight and cruise at energy use of less than 1.7 kWh/mi (equivalent to 102 kW at a cruise speed of 60 mph).
Based on these figures and the weight of a fully-loaded truck (82,000 lb = 37.2 t) we can conclude that Tesla Semi’s powertrain and batteries enable a peak mechanical power of around 660 kW (which is consistent with the total nominal power of the powertrain, equal to 750 kW and 88% efficiency at acceleration). This means that the battery pack can sustain nearly 1 MW of power at least for short periods of time. Thanks to the minimal weight of each motor (45 kg), the total weight of all three motors plus inverters, cables, and transmission (460 kg), is still much less than the weight of an average Semi truck diesel engine (1,300 kg).
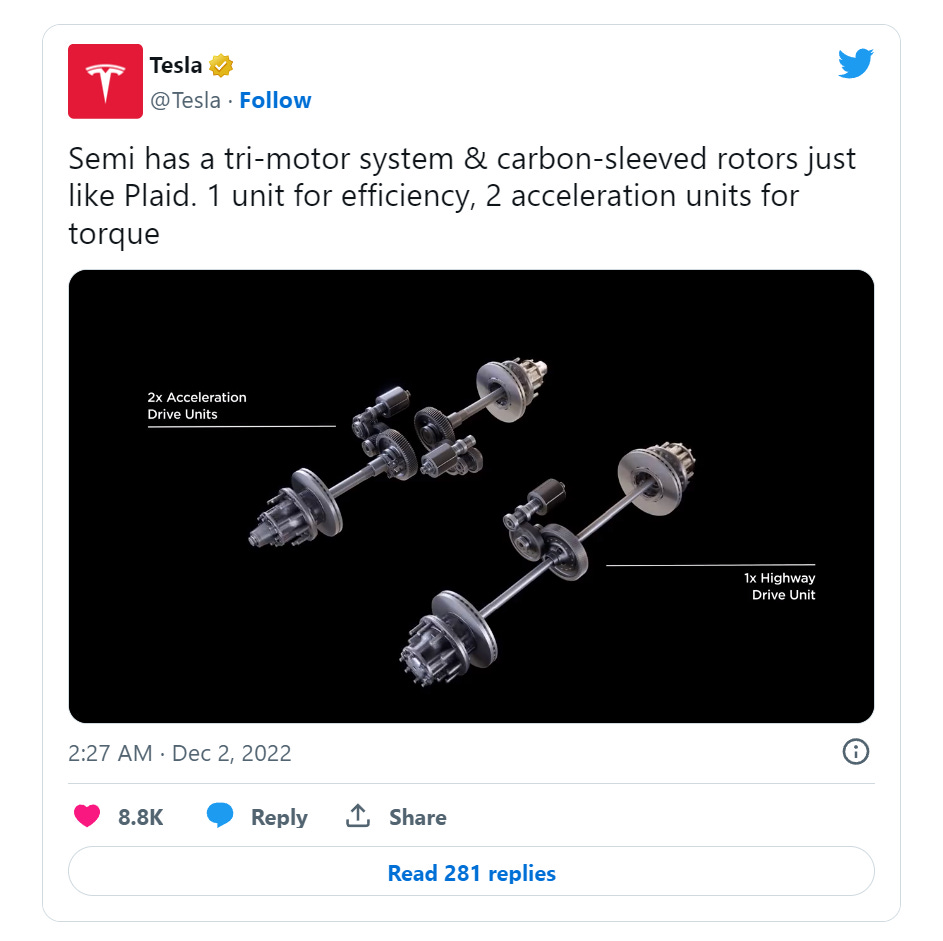
Another way to estimate the maximum power that Semi’s batteries and cables can handle is to consider the maximal charging speed. The company announced the development of a high-powered water-cooled charger for their Semi, called the Megacharger, that would provide 400 miles of range in 30 minutes, or ⅘*850 kWh/0.5 h = 1.360 MW electric power.
This power compares to that of a utility aircraft like the DHC-6 Series 300 Twin Otter 20-seater. Its two turboprop engines provide 1,020 kW of total maximal mechanical power. Provided the high efficiency of electric engines (80% conservative assumption), this power could be provided by an electric powertrain consumption of 1.3 kW. We should be careful when comparing power requirements for an EV and an electric aircraft since aircraft batteries must withstand high power much longer: while the truck's cruising power drops 7.5x down to 102 kW, the aircraft's power drops only 2x: down to about 500 kW. Still, the duration of Tesla Semi charging by means of the Megacharger (30 minutes) makes us think that in aviation the battery heating problem can be solved effectively at least for utility and regional aircraft.
Aerodynamics
Tesla has made significant strides in improving the aerodynamics of its vehicles, a factor that greatly impacts fuel efficiency. The Tesla Semi's design minimizes drag, allowing it to use less energy to maintain speed. The drag coefficient Cd for this vehicle is reported to be 0.36. Having in mind the frontal area (A=10.77 sq.m), and air density ρ=1.225 kg/m3, we can estimate the power expended on air resistance at a cruise speed of V=60 mph:
This is in agreement with recent independent modeling results, which resulted in 54.6 kW of power at 30 m/s (should scale down to 38.9 kW at a lower speed of 60 mph = 26.8 m/s ).
Now let's take the average efficiency of Tesla’s electric powertrain (90%), and total electric energy consumption at cruise speed (102 kW), to find the cruise mechanic power, 91.8 kW. This means that the power consumed for non-aerodynamic friction (tires, transmission, gears) equals 91.8 kW - 38.9 kW = 52.9 kW. We come to the conclusion that 57.6% of mechanical power is spent on friction and 42.4% on drag force counteraction. According to Tesla, a good diesel semi truck has a drag coefficient equal to 0.65. With this coefficient, i.e. without shape optimization, Tesla Semi would spend 38.9 kW*(0.65/0.36)= 70 kW. Only this factor would increase the total mechanical power by 34%. In other words, compared to less aerodynamically efficient semis Tesla Semi will use 1/(1+0.34)=0.75 of energy, 25% improvement.
Energy Efficiency & Regenerative braking
Electric engines are almost twice as energy-efficient as diesel ones (85% vs 48%). Thanks to its innovative design (for example, the use of motor units dedicated to each acceleration phase), Tesla EV energy provides even more benefits: peak efficiency is about 93%, and average efficiency is estimated at 90%.
To estimate quantitatively the contribution of regenerative braking to the total efficiency, we studied the battery discharge curve in the Tesla Semi test drive. We replaced the moments of regeneration when the track went down the mountain with horizontal sections (see the red curve in Fig.1 in the main text) as if instead of regeneration, excess energy was converted into heat in the brakes or in moving parts of the engine. The modified energy curve dropped to the discharged level (4%) 70 miles earlier than in the actual test drive (14% of the distance). At this distance, the real Tesla Semi which takes advantage of regeneration (blue curve), still had a 12.5% charge left.
Weight and transportation cost
Earlier in the main text, we estimated the weight of the battery pack to be 4,6 t (metric tons). Together with the powertrain weight it would total 5,05 t. We can see that powertrain+battery weight is dominated by the battery, which is the opposite of diesel trucks, where powertrain+fuel weight is dominated by the engine (equals to 2+0.5 t on average). The combined weight of the Tesla Semi propulsion system still exceeds that of a diesel semi truck by about 2.5 t.
Now let us find out how does it affect the cost of transportation. Based on Tesla’s empty trailer+truck weight estimate of 37,000 lb (powertrain+ batteries included), against 35,000 lb for a diesel 18-wheeler. Electric semis have an extra 2,000 lb in their weight limit, so Tesla Semi’s freight weight is almost the same as that of a regular semi: 45,000 lb or 20.4 t.
This idea is visualized in the diagram below. We, therefore, can conclude that, if Musk’s aim at 1.26 $/mile will come to a reality, Tesla Semi will outperform regular trucks of the same class based on the cost/(kg*km) metric.
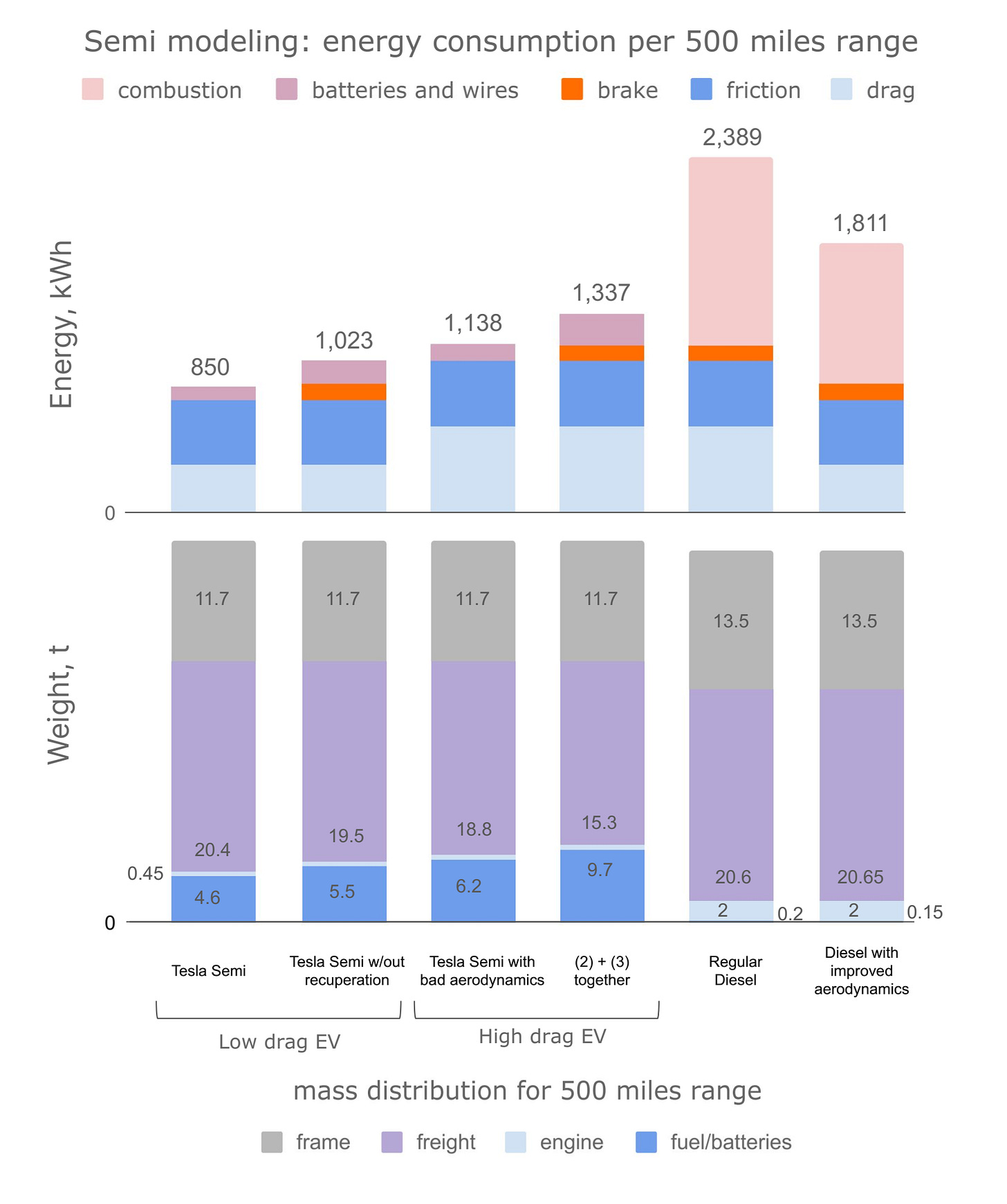
Synergetic effect of Tesla’s EV innovations
In Tesla Semi, each part, from the battery to the aerodynamic design, works together to improve the vehicle’s overall performance. One example that can spot this synergy is regenerative braking efficiency. It relies on the capability to return excess mechanical energy back to batteries at every moment. If the charging current, or the electric motor's maximal power would be limited, batteries would take only part of the excess mechanical energy.
Here are the calculations to support our point. As we have seen above, the battery pack is estimated to have a total weight of 4.6 t. Out of this mass, only a part is due to the cell: the rest is the cooling, wiring, and frame. We can find the mass of all 2170 cells in the pack if we know the cell-level and pack-level energy densities:
Now we can calculate the specific power, required at the peak energy power 750 kW: p=220 W/kg. Looking at the 2170 cell Ragone plot below we see, that this specific power lies in the flat part of the plot, meaning that the cell can simultaneously ensure both nominal specific energy and the desired specific power.
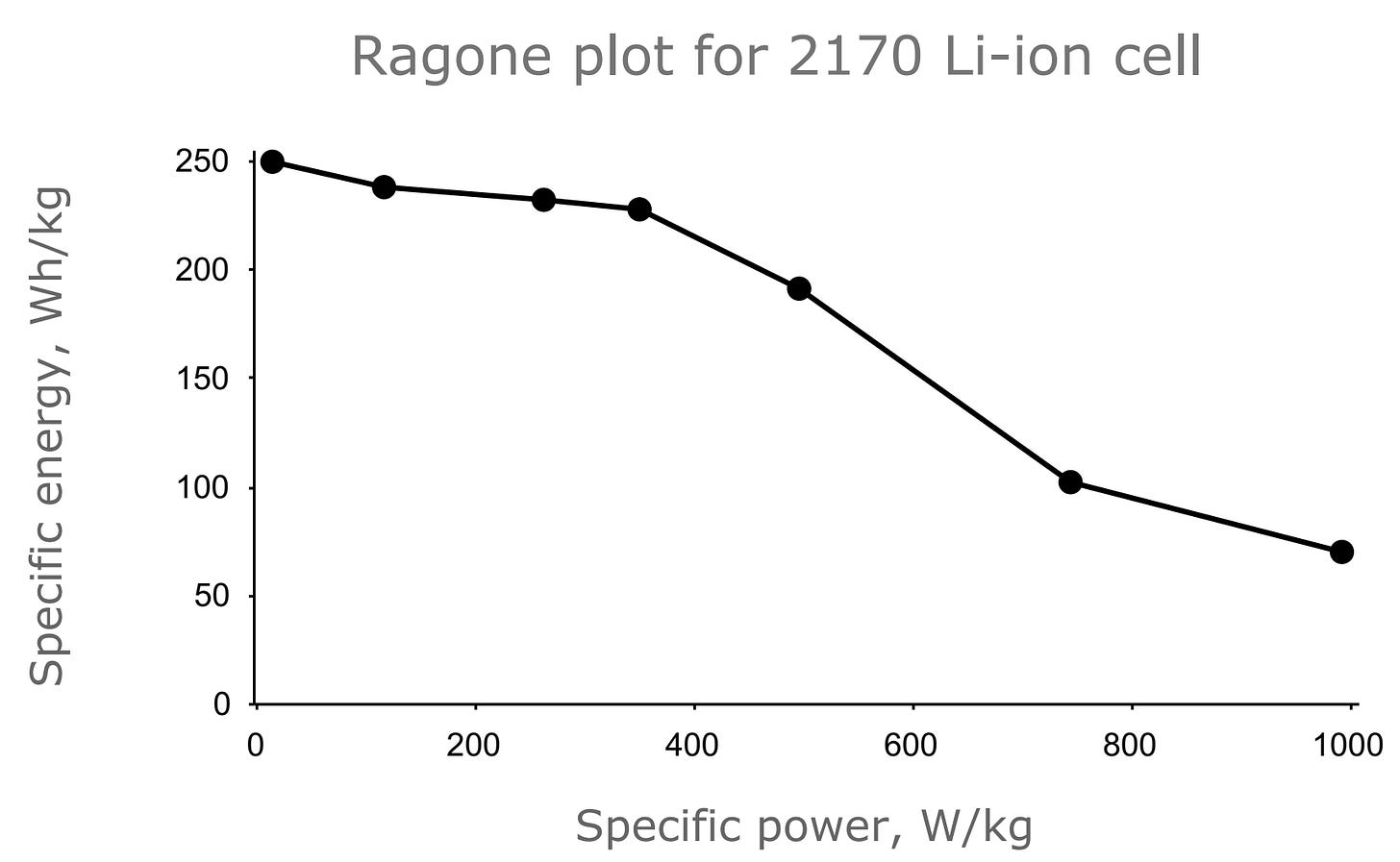
A smaller battery pack would mean a higher power/mass value, which would result in either lower specific energy, or programmed input power limitations. The latter would mean that we can’t recuperate all the power during braking.
One more example of synergetic design improvements is the use of multiple engine units to enhance overall energy efficiency. As the mass of the battery pack is inversely proportional to the engine efficiency, each percent of energy efficiency reduces the battery pack weight by approximately 50 kg:
We suppose that the introduction of two additional motor units (90 kg) helps to maintain the high regeneration power and also allows to use of the optimal motor at each acceleration step, thus returning more than 2% efficiency. Thanks to the extremely low weight of each additional motor unit, their use actually reduces the overall truck weight.
New EVs in EU emit pedestrian noise starting today, London mulls ‘futuristic’ e-bus noises. Phil Dzikiy for Electrek, July 1, 2019
U.S. finalizes long-delayed 'quiet cars' rule, extending deadline. David Shepardson for Reuters, July 1, 2019
Vehicle weight classes & categories. US Department of Energy. June 2012
Tesla Semi defies laws of physics and is passing us by if true, says Daimler’s head of trucks. Fred Lambert for Electrek, February 21, 2018
Tesla Semi driving 500 miles, fully loaded, on a single charge on YouTube, December 2, 2022
How do we move around in a zero-carbon world? Bill Gates for Gates, August 24, 2020
Tesla to use iron-based batteries in Semi electric trucks and affordable electric car. Hyunjoo Jin and Paul Lienert for Reuters, July 1, 2020
Exclusive: Panasonic aims to boost energy density in Tesla batteries by 20% - executive. Makiko Yamazaki for Reuters , July 30, 2020
The Tesla Semi: Why Now? // The Road to Commercial Viability on The Limiting Factor YouTube channel, February 19, 2023
From Cell to Battery System in BEVs: Analysis of System Packing Efficiency and Cell Types. Hendrik Löbberding et al. in World Electr. Veh. J., 2020
4680 Battery Pack: What We Found Under the Foam! Sandy Munro on YouTube, July 27, 2022
All about semi-truck fuel efficiency. Phoenix, August 12, 2022
Thermally modulated lithium iron phosphate batteries for mass-market electric vehicles. Xiao-Guang Yang, Teng Liu & Chao-Yang Wang in Nature Energy, January 18, 2021
Semi has a tri-motor system & carbon-sleeved rotors just like Plaid. 1 unit for efficiency, 2 acceleration units for torque. Tesla on Twitter, December 2, 2022
Watch Dissection Of Tesla Model S Plaid Front Drive Unit. Mark Kane for InsideEVs, October 26, 2021
DHC-6 Twin Otter Series 400. De Haviland Aircraft of Canada Limited, 2021
Pratt & Whitney Canada PT6A-27 Type Certificate Data Sheet. US DOT FAA, December 21, 2012
Battery research for vertical take-off and landing aircraft takes off. The Faraday Institution, July 1, 2021
Reshaping electric aircraft. Tidal Wave on Substack, January 17, 2023
The ever-improving efficiency of the diesel engine. Nic Lutsey for ICCT Blog, August 14, 2015
Completed at highway speed, without charging on the way & over 4,000 ft of elevation. Tesla on Twitter, December 2, 2022
The total impracticality of electric aviation, Tad McGeer sUAS News 28 April 2023
Tesla Battery Day on YouTube, September 22, 2020
Tesla makes progress on 4680 battery cells, reduces dependence on them. Fred Lambert for Electrek, October 20, 2020
Current efficiency is 1.7kWh/mile, but there is a clear path to 1.6, possibly 1.5. Elon Musk on Twitter. December 02, 2022
Master Plan Part 3. Tesla, April 5, 2023
2022 Tesla Semi Specifications. Battery Design, December 15, 2022
Know your tools - The truckers guide to truck engines. United World Transportation, 2023
Tesla Semi Delivery Event on YouTube, December 02, 2022
Tesla Semi & Roadster Unveil on YouTube, December 14, 2017
TESLA SEMI Aerodynamic simulation report by Airshaper, April 21, 2022
Our best clue to date for the weight of the 500 mile Tesla Semi. Nikola Insider on Twitter, November 30, 2022
How much does a semi truck weigh? Onsite Truck & Equipment Repair, 2023
Panasonic TESLA Model 3. Batemo GmbH, 2023